As a homeowner who has faced the frustration and anxiety of dealing with a leaking roof, I understand the urgency and stress that comes with addressing this common household issue. A leaking roof not only compromises the integrity of your home but can also lead to costly water damage and mold growth if left untreated.
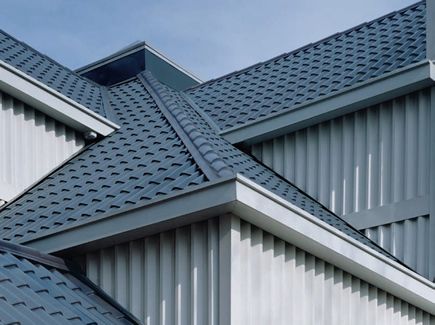
In this Roofing Santa Ana CA guide, I’ll share practical steps and tips on how to identify, diagnose, and repair a leaking roof, empowering homeowners to tackle this challenge with confidence and effectiveness.
Identifying the Source of the Leak:
- Interior Inspection: Begin by conducting a thorough inspection of the interior of your home to identify signs of water intrusion. Look for water stains on ceilings, walls, and around windows and doors, as well as any dampness or discoloration in attic spaces. Follow the path of the water stains to trace the source of the leak back to the roof.
- Exterior Examination: Once you’ve identified potential leak areas from inside, it’s time to inspect the exterior of your roof. Look for missing, damaged, or lifted shingles, as well as cracks or gaps in flashing around chimneys, vents, and skylights. Check for debris buildup in gutters and downspouts, which can block water flow and contribute to leaks.
- Attic Inspection: If accessible, conduct an inspection of your attic space to assess the condition of the roof deck and insulation. Look for signs of moisture, such as water stains, mold growth, or rotting wood. Use a flashlight to inspect the underside of the roof for any visible signs of leaks or damage.
Repairing the Leak:
- Temporary Measures: If you discover an active leak, take immediate action to minimize water damage by implementing temporary measures. Place buckets or containers to catch dripping water and use towels or mops to soak up excess moisture. If possible, apply roofing cement or patching material to temporarily seal the leak until permanent repairs can be made.
- Replacing Damaged Shingles: If the leak is caused by damaged or missing shingles, carefully remove the affected shingles using a pry bar or hammer. Replace them with new shingles of the same type and color, ensuring proper alignment and secure fastening. Seal the edges of the new shingles with roofing cement to prevent water infiltration.
- Repairing Flashing: Flashing is a common source of roof leaks, especially around chimneys, vents, and skylights. To repair flashing leaks, carefully remove the damaged or deteriorated flashing using a pry bar or utility knife. Clean the area thoroughly and install new flashing, ensuring a tight seal around the penetration. Secure the flashing with roofing nails or screws and apply roofing cement to seal the edges.
- Sealing Roof Penetrations: Roof penetrations such as vents, pipes, and chimneys are vulnerable areas for leaks. Inspect the seals around these penetrations for signs of cracking or deterioration. Apply roofing caulk or sealant to seal any gaps or cracks and prevent water infiltration. For added protection, consider installing a flashing boot or collar around roof penetrations to provide a watertight seal.
- Repairing Roof Deck Damage: In cases where the leak has caused damage to the roof deck or underlying structure, repairs may be more extensive. Carefully remove any damaged or rotted wood and replace it with new decking material. Ensure proper ventilation and insulation to prevent future moisture buildup and deterioration.
- Professional Assistance: For complex or extensive roof repairs, or if you’re unsure about tackling the job yourself, it’s advisable to seek professional assistance. A qualified roofing contractor can assess the extent of the damage, recommend appropriate repairs, and ensure that the work is completed safely and effectively.
Preventive Maintenance:
- Regular Roof Inspections: Schedule regular inspections of your roof, ideally once or twice a year, to identify and address potential issues before they escalate into leaks. Look for signs of damage or wear and tear, such as loose or missing shingles, damaged flashing, or debris buildup in gutters.
- Prompt Repairs: Address minor issues promptly to prevent them from becoming larger problems. Don’t ignore small leaks or damage, as they can worsen over time and lead to more extensive water damage and costly repairs.
- Gutter Maintenance: Keep gutters and downspouts clear of debris to ensure proper water drainage from the roof. Clean gutters regularly and inspect them for damage or sagging. Consider installing gutter guards to prevent debris buildup and reduce maintenance requirements.
- Trim Trees and Branches: Trim overhanging trees and branches that could potentially damage your roof during storms or high winds. Branches that come into contact with the roof can cause abrasion, punctures, or dislodged shingles, leading to leaks and structural damage.
Conclusion:
Overall, based from Roofing Santa Ana CA, dealing with a leaking roof can be a stressful and daunting task, but by following these steps and tips, homeowners can effectively identify, diagnose, and repair roof leaks. Remember to conduct thorough inspections, address issues promptly, and prioritize preventive maintenance to safeguard your home against future leaks and water damage. If in doubt, don’t hesitate to seek professional assistance to ensure that repairs are completed safely and effectively. With proactive maintenance and timely repairs, you can maintain a watertight roof that protects your home for years to come.
Best Roofing Solution – Santa Ana
2429 W Elder Ave, Santa Ana, CA 92704, United States
714-451-4926